Importance of Flow Meters
- By Park Yin
- •
- 26 Dec, 2017
- •
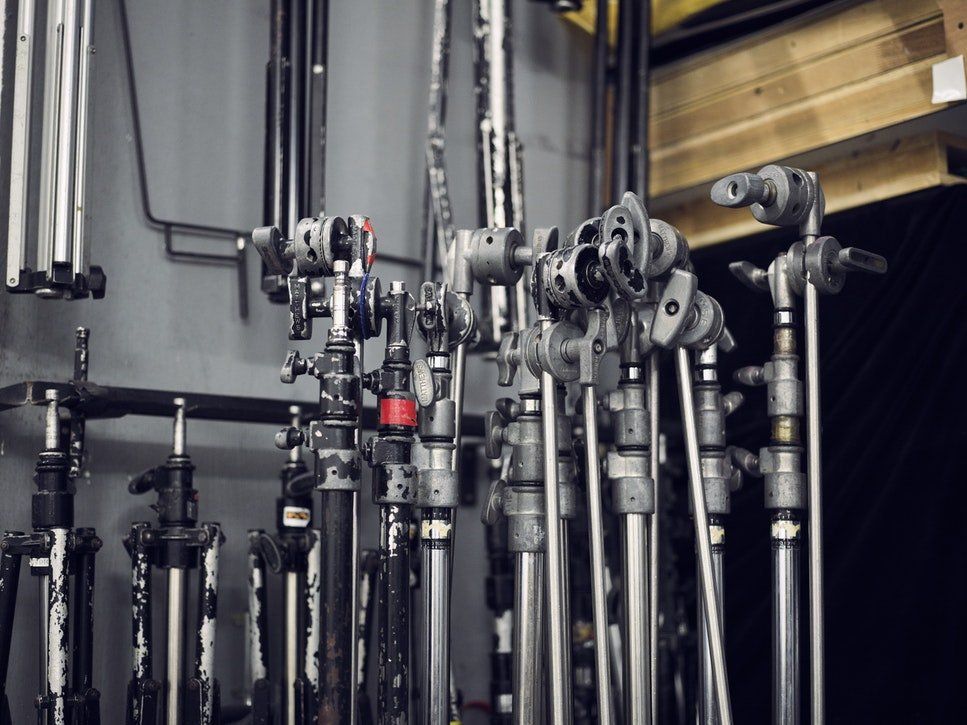
Flow meters are an important component of virtually every oil and gas operation. But at gathering facilities, where custody of tens of millions of gallons of product is transferred from one party to another on a daily basis, their role is mission-critical. Consider, for example, a gathering station that pumps 10,000 gallons of crude oil per minute. A flowmeter measurement error of just 0.02% (under what is actually being pumped) will result in the loss of 68 barrels per day. At $40 per barrel, that translates into nearly $1 million per year.
Taking proactive steps to ensure that flowmeters perform accurately and reliably is key to avoiding this. The first, and perhaps most important, action to help prevent measurement inaccuracy is to make sure that instrumentation is properly calibrated before it is put into operation. In today’s market, there are hundreds of different measurement options that operators can choose from (Coriolis, ultrasonic, vortex, rotameters, etc.), and while many employ highly advanced technologies, the benefits they provide can only be realized if they are properly commissioned. In most cases, errors made during pre-operational phases will also lead to complications down the road, such as higher maintenance costs and more downtime.
Because flow meters are often in continuous use, drifting can also be a serious problem. Periodic meter proving is essential to identifying drift and correcting it. Flow meters indicate volume by producing pulses in proportion to the amount of fluid that passes through them (more pulses means higher volume). Meter proving is a type of calibration that uses this concept to determine accuracy by comparing a known volume of liquid passed through a prover to the volume indicated by the flow meter being tested. The data obtained during the proving test is used to calculate a correction, which allows operators to adjust meter readings so that they are representative of true flow rates.
Routine meter proving / calibration also helps protect against measurement inaccuracies arising from natural mechanical wear, product build up, pipe blockages, and changes to the properties of the product flowing through the line.
One method of Mass Flow measurement employs the phenomenon of Coriolis force. This force is a deflection of moving objects when they are viewed in a rotating reference frame. Coriolis force is proportional to the rotation rate and the centrifugal force is proportional to its square.
This long understood principle is all around us in the physical world; the flow of water down the sink, the Earth’s rotation and its effect on the weather. The principle, and mathematical formula developed back in the 1800’s, was further developed during the 1970’s and then applied to the measurement of fluid flow. The operating principle is basic but very effective. A tube, or tubes, with a known mass is energized by a fixed vibration. When a fluid passes through the tube(s) the mass will change, the tube(s) will twist and the inlet and outlet sections will result in a phase shift. This phase shift can be measured and a linear output derived proportional to flow. As this principle simply measures whatever is within the tube it can be directly applied to any fluid flowing through it, liquid or gas. Furthermore, in parallel with the phase shift in frequency between inlet and outlet it is also possible to measure the actual change in frequency. This change in frequency is in direct proportion to the density of the fluid – and a further signal output can be derived. Having measured both the mass flow rate and the density it is, interestingly, therefore possible to derive the volume flow rate.